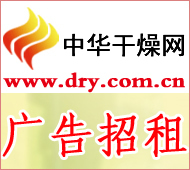
In 2011, the development of Yueyang Petrochemical Industry became Yueyang's first 100 billion yuan industry, with an output value of 103.8 billion yuan and a tax revenue of 9 billion yuan. In the past year, we have been striving for Sinopec to expand investment in Yue and to allocate more projects. Since the “Eleventh Five-Year Planâ€, Sinopec has invested RMB 9.5 billion in Yueyang, and a number of major projects and good projects have been settled in Yueyang. The second is to encourage technological innovation. Establish a petrochemical industry technology alliance and set up a "Yueyang petrochemical industry technology innovation project" to support enterprises in overcoming major key technologies and bottleneck technologies in the petrochemical industry and developing new products and new processes. The third is to ensure the supply of factors. During the orderly power supply last year, we fully safeguarded the demand for electricity in Changling Refinery and Baling Petrochemical. We did not provide once-a-day power for enterprises, and limited one day to ensure that enterprises have full production and long-term operation. Push the product toward both ends. Relying on the resources and market of Changling Refinery and Baling Petrochemical, we will do a good job in petrochemical industry chain investment and supporting investment, and promote localization of Dachang products. The second is to promote enterprises to gather in the park. Promote enterprises to enter the park in groups, gather development, successfully created the Yunxi Fine Chemical Industry Park, Changxing Specialty Chemical Park, Linxiang Ruxi Chemical Industrial Park. The third is to promote the facilities to the industry. We will focus on establishing a large service platform to promote infrastructure support to the industry and provide a strong foundation for the development of the petrochemical industry.
Hot Cutting Extrusion Pelletizer
LINA Extrusion Pelletizer
Most of the polymer must be kneaded and then granulated before it is made into a final product. Sorted by pelletizing ways, LINA rubber & plastic granulator can be divided into four categories: 1. Hot-cutting and air-cooling pelletizing method. 2. Under-water granulating method. 3. Water-strand extrusion method. 4. Water-ring granulation method. LINA pelletizer can meet the granulation needs of high-viscosity and low viscosity rubber and plastic materials, as well as some new materials and chemical additives.
LINA Die Surface Hot Cutting Pelletizing Machine
LINA`s die surface hot cutting and air cooling granulating machine is suitable for polymers that are sensitive to heat and long residence time, such as PVC, TPR, PE, cross-linked PE and so on. The flow path of the polymer from the extruder to the pelletizing port should be kept as short as possible with minimal heat. When polymer is extruded through the die surface, the rotating blade cuts the extruded materials into particles. After the pellets are cut, they are removed from the rotary blade and caught by cooling air circulating in the pelletizing room. The air stream preliminary cools the surface of the pellets and takes them out of the pelletizing room and sends them to the cooling zone.
Assembly Ling Diagram of LINA Die Surface Hot Cutting Granulator
Advantage of LINA Pelletizing Line
1. The unit has the whole unit process chain, sound and light failure alarm and fast lock fault point and other control functions. All parts that are in contact with the material are made of stainless steel.
2. High accuracy of temperature control system to ensure the temperature sensitivity of the material.
3. It adopts the drop type separating method after cutting process, to avoid Particle agglomeration and ensure particle cooling.
4. Feeding system of the pressing machine adopts heater and reversing device to solve problem of power outage, material crash and cleaning.
5. Especially, the barrel and die head adopts advanced foreign techniques to ensure and control the dangerous occurred when the pressure is uncontrollable. The honeycomb filter plate is easy to clean and quickly change the mesh and the die head t easy to leak.
6. The hoist adopts automatic return technology to ensure the working efficiency.
7. The technological combination of dual-pull forced feeder and single screw not only meet the high requirement of secondary continuous mixing, but also solve the problem of time and power consuming of traditional working process.
Specifications of LINA Extrusion Granulating Line
Name |
Mode |
Capacity of Kneader |
Screw length to diameter ratio |
Screw diameter |
Dimension |
LINA Extrusion Pelletizing Line |
LN-10/70 |
10L |
12:01 |
70mm |
2200*1000*1150 |
LN-10/75 |
10L |
12:01 |
75mm |
2650*1100*1250 |
|
LN-35/100 |
35L |
12:01 |
100mm |
3800*1090*1690 |
|
LN-55/120 |
55L |
12:01 |
120mm |
3800*1090*1690 |
|
LN-75/135 |
75L |
12:01 |
135mm |
3850*2350*3280 |
|
LN-110/150 |
110L |
12:01 |
150mm |
5100*2000*1500 |
|
LN-110/165 |
110L |
12:01 |
165mm |
5100*2000*1500 |
Hot Cutting Pelletizer,Hot Cutting Pelletizing Line,Hot Cutting Pelletizing Machine,Plastic Hot Cutting Granulator
LINA Machinery Industrial Co.,Ltd , https://www.linakneader.com